How SLA/DLP 3D Printing is Transforming High-Performance Manufacturing
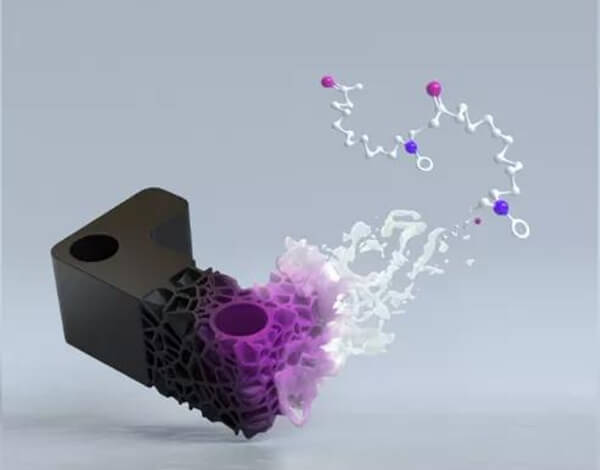
Resin-based 3D printing technologies—Stereolithography (SLA) and Digital Light Processing (DLP)—have rapidly evolved into industrial manufacturing solutions. Once used primarily for prototyping, SLA/DLP now compete with traditional manufacturing methods by offering exceptional precision, fast production speeds, and a wide range of high-performance materials.
With advances in photopolymer chemistry, SLA/DLP can now produce strong, durable, and heat-resistant parts, making them viable alternatives to injection molding and powder-based AM methods like SLS or Multi Jet Fusion (MJF).
Why Manufacturers Are Adopting SLA/DLP
SLA and DLP both use photopolymerization, where liquid resin is selectively cured by UV or visible light. This enables:
- Unmatched Resolution & Surface Quality – Layer heights as fine as 25 µm create smooth, highly detailed parts with minimal post-processing.
- Faster Print Speeds – DLP’s area-wide exposure mechanism significantly reduces build time compared to laser-based systems.
- Stronger, Isotropic Parts – Unlike FDM, where layers can delaminate, SLA/DLP parts maintain uniform strength in all directions.
- Quick Material Swaps – Unlike powder-based AM methods, SLA/DLP resins can be switched in minutes, allowing manufacturers to use multiple materials in a single workflow.
- Expanding Material Selection – SLA/DLP resins now include high-toughness, flexible, heat-resistant, and ceramic-filled options, rivaling thermoplastics.
Advancements in SLA/DLP Resin Technology
Early SLA/DLP materials were brittle and limited to prototyping, but today’s resins offer mechanical and thermal performance comparable to traditional polymers.
Key Resin Advancements:
- High-Impact & Tough Resins – New formulations exceed 100% elongation at break, making them viable for dynamic and load-bearing applications.
- Heat-Resistant Resins – SLA/DLP now offers materials with heat deflection temperatures (HDT) over 300°C, enabling applications in aerospace, automotive, and industrial tooling.
- Wear-Resistant Ceramic Composites – Nano-ceramic and glass-filled resins enhance rigidity, durability, and thermal stability, making them excellent for high-precision tooling.
- Castable & Burnout-Optimized Resins – High-wax-content SLA/DLP resins now support investment casting for jewelry, dental, and industrial applications.
These advancements make SLA/DLP a strong alternative to injection molding, powder-based AM, and even CNC machining in some cases.
Key Applications of SLA/DLP in Industry
With expanded material options, SLA/DLP is now a production technology across multiple industries.
1. Aerospace & Automotive
- Heat-Resistant Resins – SLA/DLP materials with high HDT values maintain structural integrity in extreme environments.
- Flame-Retardant Materials – Resins meeting UL94 V-0 and Airbus FST standards allow for interior and under-the-hood components.
2. Medical & Healthcare
- Biocompatible Resins – SLA/DLP is now used for patient-specific medical devices, prosthetics, and surgical guides.
- Silicone-Like Elastomers – Soft-touch materials allow for realistic anatomical models and wearable medical devices.
3. Industrial Tooling & Manufacturing
- Wear-Resistant, High-Strength Resins – Ideal for jigs, fixtures, and short-run injection molds.
- Functional Prototypes & Custom Parts – SLA/DLP enables precision prototyping and on-demand production of industrial components.
SLA/DLP for Agile, Cost-Effective Manufacturing
With increasing demand for low-volume, on-demand production, SLA/DLP provides cost-effective alternatives to traditional AM and injection molding.
Business Advantages of SLA/DLP:
✅ Less Material Waste – SLA/DLP uses liquid resin efficiently, unlike powder-based AM, which requires sieving and recycling excess material.
✅ Faster Turnaround – DLP’s area-wide curing significantly reduces build time, making it faster than SLS or FDM for many part geometries.
✅ Simplified Post-Processing – SLA/DLP only requires washing and UV curing, avoiding the complex powder removal required in SLS/MJF.
✅ Flexible, Multi-Material Production – Rapid material swaps allow for customization and batch production without lengthy downtimes.
The Future of SLA/DLP in Manufacturing
With significant advancements in material strength, durability, and high-temperature performance, SLA/DLP is now a full-scale production technology across industries. As photopolymer chemistry continues to evolve, manufacturers will increasingly rely on SLA/DLP for fast, precise, and cost-effective production.
Leverage SLA/DLP for Your Next Project with RapidMade
At RapidMade, we specialize in high-performance SLA/DLP 3D printing for aerospace, medical, and industrial applications. Whether you need functional prototypes, low-volume production, or end-use parts, we provide cutting-edge photopolymer solutions to meet your needs.