Exploring the AISC Design Flow in VLSI
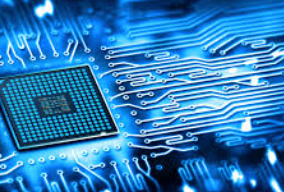
The AISC design flow refers to the complete procedure and methodologies from conception to production of integrated circuits in a vlsi design system. It can be considered as a guidebook that engineers follow to develop integrated circuits from abstract concepts to fully functional and practical chips. The design flow has a procedural fashion in the development of integrated circuits, that ensures efficiency and reliability in chip development. As a result, the development of more complex and high-performance ICs becomes easy. This paper covers the details of the AISC design flow and its importance in VLSI.
The specification stage
The design should not be initiated without first determining the specifications of the integrated circuit that should be produced. This requires assembling and thoroughly documenting all of the relevant information, such as the prospective functionality, expected performance metrics, power constraints, and macroscopic dimensions. The idea of having well-defined and thorough specifications is critical since they will be utilised in the remaining stages to ensure that the final design remains faithful to the intended principle.
Architectural design
The architectural design phase. Here, engineers draw the big picture of how the integrated circuit in question should be structured and organised. They decide on the different functional blocks, how they should be intertwined, what data will flow where, etc. All this is a very high level of the IC design “skyscraper,” but even here the devil is in the details. Performance, power, and area: these are the main ingredients of the design that should perfectly counterbalance each other.
Logic design
The next step of the chip development process for vlsi chips is logic design. It involves compiling the architectural specifications into a complete definition of the digital logic circuits. Computer engineers use hardware description languages, such as Verilog, VHDL, etc., to describe the logical operation of the chip. It consists of the design of combinational and sequential logic circuits, finite state machines, and all other elements needed to have the IC.
Functional verification
Before going any further, it is vital to ensure that the design is functionally correct. At the functional verification level, engineers use simulation tools and test benches to completely examine the logic design against its defined requirements. This method ensures all possible logic errors are detected and corrected, giving the design its integrity and protecting it from expensive mistakes at subsequent stages.
Synthesis and optimization
The third stage is called the synthesis and optimization stage. The purpose of this stage is to translate the abstract logic design into a gate-level representation. Synthesis tools evaluate the HDL code and find the optimal way to implement the logic. They optimise the netlist using different methods to reduce area, power, timing violations, etc., to make the gate-level netlist as efficient as possible.
Physical design
After receiving the gate-level netlist, the physical design stage can begin. It is the stage during which the circuit layout is made, and the individual elements of the circuit are placed and routed on the surface of the chip. During this stage, all placement and routing are made with caution to optimise the aforementioned areas. Floor planning, placement, and routing are all dependent on one another because only well-made floor planning can lead to efficient placement and routing.
Design verification
The next required step of verification is the AISC design flow design. In this step, the design verification stage physical layout should be rigorously verified if there are potential issues in the timing, signal integrity, or any other layout-related rule violations. Static verification and dynamic verification should be performed, and no more remaining issues should be present, before moving to the next stage.
Mask generation
With the physical layout validated, the next phase is mask generation to prepare the design for fabrication. To be precise, the layout data are used to generate photomasks, which play the critical role of enabling the projection of circuit patterns on the silicon wafers. Since it has already been mentioned that the chip is an impression of one’s design, mask generation is a critical aspect of the generation process. During manufacturing, the photomasks act as a projection clearing the way for light projection or radiation through the silicon shaving patterns for deposition and etching.
Fabrication and testing
The third stage involves the actual physicalization of the integrated circuit. Such production occurs at a semiconductor fabrication foundry, also known as a fab. The fabrication process is complicated and includes such steps as deposition, lithography, etching, doping, and many other steps to print the structure of the circuit on silicon wafers. Once the wafers are produced, the chips are tested to make sure they work and meet certain criteria. Therefore, the fab and test processes should create conditions for quality control of any expected human factors and the ability to produce a high-enough output of reliable and working integrated circuits.
Post-Silicon validation
Even following the creation and testing of the material, the AISC design retains a “post-silicon validation” stage. This “stage” consists of months of feeding the real-world test results into the simulation, refining it to reach all the operational criteria, and ensuring that the manufactured chip behaves as expected. Additionally, should any problems or inaccuracies be found in the chip’s operation, they can be fixed through the alteration of the design or a simple software patch, improving the chip’s reliability and performance even further.
Continuous improvement
The AISC design flow cycle is a repetitive process with room for improvement at each step. As newer technologies arise and design paradigms mature, engineers can leverage best practices, sophisticated tools, and creative strategies to improve the efficiency, quality, and speed-to-market of their integrated circuit designs. Furthermore, the AISC design flow is a cycle model, and it can be custom-made to incorporate innovative paradigms, making it trendy and modifiable for the innovative chip-making environments, which allows for the efficient development of modern complex high-performance integrated circuits.
See also: Identity Theft Protection: Shield Firms Against Telecom Fraud
Conclusion
The AISC design flow is a well-structured and organised method to design and fabricate chips for integrated circuits in the VLSI sector. The steps from the specification gathering to post-silicon validation serve various functions in ensuring the successful implementation of high-performance, low-power, reliable, and cost-effective chips. By following the flow, engineers can easily organise their design efforts, minimise errors, and come up with product designs that demonstrate the high standards demanded by the rapidly evolving electronics industry. As technology evolves, the AISC design flow will undergo updates to help produce far more complex integrated circuit designs and embedded system solution that will increasingly fuel advancements in the electronics world.